When left unchecked, electrical equipment becomes a silent risk in any workplace. Cords fray, insulation wears down, and faults creep in unnoticed—until they spark a problem. Testing and tagging aren’t just a checkbox for compliance; they’re a frontline measure that keeps work environments safe and operations running smoothly. Testing electrical equipment regularly ensures potential issues are identified and addressed before they cause harm or disruption.
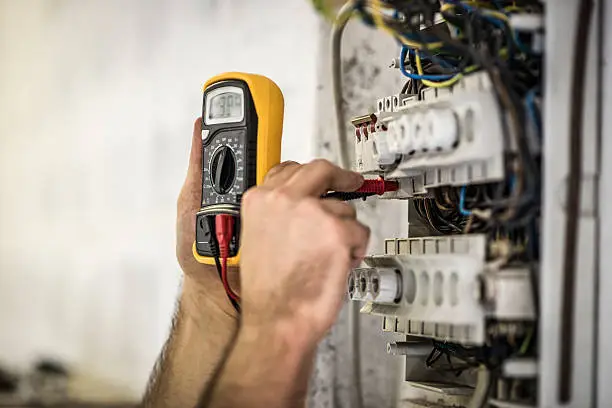
This article offers practical, environment-specific advice to help businesses meet safety standards, prevent downtime, reduce liability, and build a routine that protects people and equipment from everyday hazards.
Schedule Regular Inspections
Regular inspections are key to detecting potential hazards early. The testing frequency should match the environment where the equipment is used.
High-Risk Environments
Equipment often undergoes harsh treatment in high-risk locations like construction sites or demolition areas, increasing the risk of electrical faults.
- Testing Frequency: Every 3 months
- Examples of Equipment: Power tools, extension cords, temporary lighting
- Reasoning: Constant movement, rough use, and outdoor exposure increase the need for frequent checks
Maintaining a strict schedule can greatly reduce the risk of serious faults, helping avoid on-site accidents and downtime.
Moderate-Risk Environments
Places like mechanical workshops or warehouses fall into a medium-risk category. While safer than construction zones, risks remain due to heavy equipment and machinery use.
- Testing Frequency: Every 6 months
- Examples of Equipment: Stationary tools, fixed industrial machines, workbenches with electrical components
- Reasoning: Periodic movement and general wear make semi-annual testing necessary to spot emerging issues
A biannual inspection routine balances safety and practicality in these settings.
Low-Risk Environments
Office spaces, retail areas, and administrative buildings typically use electrical equipment with lower risk exposure.
- Testing Frequency: Annually
- Examples of Equipment: Computers, monitors, printers, toasters, kettles
- Reasoning: Limited movement and use mean electrical issues are less frequent, allowing for longer intervals between tests
Even in these environments, regular inspection ensures any unnoticed degradation is caught in time.
Use Competent Personnel
The effectiveness of a testing and tagging program depends heavily on the qualifications and preparedness of the personnel.
Qualifications And Training
People carrying out tests should have completed accredited training and hold valid qualifications to carry out their duties.
- Training Standards: Completion of recognised test and tag courses that cover both theory and hands-on experience
- Knowledge Requirements: Understanding of the AS/NZS 3760:2022 standard, risk assessment protocols, and electrical safety measures
- Competency Proof: Holding certification and being listed on a recognised register of test and tag professionals
Proper training ensures inspections are thorough and compliant with regulations.
Tools And Equipment
The correct tools are critical for accurate and safe testing.
- Portable Appliance Testers (PAT): Essential for conducting insulation resistance, polarity, and earth continuity tests
- Digital Recorders or Tablets: Help streamline data entry and tagging updates
- Tagging Devices: For printing and applying tags with clear, durable labels
Using reliable, calibrated tools ensures consistency and safety in every inspection.
Licensing Requirements
Although not all test and tag tasks require an electrician’s license, a licensed professional must perform repairs or assessments beyond standard testing. If issues are found during inspection should be escalated to an electrician with the authority and experience to perform the necessary repairs.
Maintain Detailed Records
Accurate and well-kept records are vital for maintaining compliance, tracking testing history, and improving workplace safety.
What To Record
Every testing and tagging instance should include:
- Identification: Device type, make, model, serial number
- Test Date: When the inspection took place
- Inspector: Name and credentials of the person conducting the test
- Test Outcome: Pass/fail result, and any notes regarding faults
- Next Due Date: Clear indication of when the next test is scheduled
Each record should be stored digitally or in an easily accessible logbook during audits.
Benefits Of Proper Documentation
- Compliance Proof: Serves as evidence during WorkSafe inspections or internal audits
- Trend Analysis: Helps identify recurring faults or problematic equipment models
- Maintenance Planning: Supports budgeting for replacements and scheduled servicing
Access to historical data improves operational efficiency and enhances decision-making around equipment life cycles.
Prioritise Safety During Inspections
Inspections carry risks, so it’s vital to implement measures that protect staff and reduce exposure to electrical hazards.
Pre-Inspection Safety Measures
Before beginning any inspection:
- Disconnect Power: Unplug equipment to eliminate the risk of shock or arcing
- Use Personal Protective Equipment (PPE): Gloves, safety glasses, and non-conductive footwear are common requirements
- Evaluate the Testing Area: Remove water sources, ensure dry surfaces, and prevent trip hazards.
Establishing a safe working environment reduces the chances of accidents during testing.
Inspection Best Practices
During the inspection:
- Follow a Checklist: Use a standard procedure to ensure nothing is overlooked
- Test in Sequence: Start with visual inspection, followed by earth continuity, insulation resistance, and polarity
- Apply Tags Securely: Tags should be legible, securely attached, and made from durable material
Sticking to a structured routine ensures consistent and reliable testing outcomes.
Post-Inspection Protocols
Once testing is complete:
- Isolate Failed Equipment: Immediately tag and remove from service any appliance that fails
- Report and Document: Notify supervisors or the maintenance team and update the central log
- Review and Plan: Check if additional equipment is due for testing and plan accordingly
Effective follow-up strengthens safety culture and ensures corrective actions are not delayed.
Additional Tips For Effective Testing And Tagging
Use A Colour Coding System
Colour-coded tags are a simple way to track testing intervals visually. Many organisations follow a quarterly colour system to identify the timing of the last test at a glance.
- Red – January to March
- Blue – April to June
- Green – July to September
- Yellow – October to December
This system helps employees and safety officers spot outdated tags quickly and avoid oversight.
In-House Testing Vs Outsourcing
Organisations may choose between internal testing and hiring an external provider.
- In-House Benefits: More control, faster response to urgent needs, lower long-term costs if volume is high
- Outsourcing Benefits: Professional expertise, access to advanced tools, compliance assurance
Some companies adopt a hybrid approach—training in-house staff for basic checks and bringing in specialists for periodic, detailed inspections.
Keep Staff Informed
Regularly update team members on tagging procedures and what to do when they find damaged or untagged equipment.
- Quick Reference Guides: Posters or cheat sheets in workstations
- Toolbox Talks: Short safety meetings to reinforce awareness
- Feedback Channels: A process for reporting issues or improvements
Creating an informed team contributes to a culture of safety and accountability.
Conclusion
Following these best practices ensures your testing and tagging program is consistent, effective, and compliant. From scheduling inspections to maintaining records and prioritising safety, every step protects workers and reduces the risk of equipment-related incidents.
By investing in trained personnel, quality tools, and clear processes, organisations meet legal obligations and foster a proactive safety culture that benefits everyone.
Frequently Asked Questions
How Often Should Electrical Equipment Be Tested And Tagged?
The frequency of testing and tagging depends on the environment where the equipment is used. High-risk areas like construction sites require testing every 3 months, while workshops should follow a 6-month schedule. Low-risk environments, such as offices, generally need annual inspections. These intervals help maintain safety and prevent electrical hazards.
Who Is Qualified To Perform Testing And Tagging?
Only individuals who have completed a recognised training course in test and tag procedures should conduct inspections. They must understand the AS/NZS 3760:2022 standard and be able to use the correct tools safely. A licensed electrician must be involved for repairs or issues beyond testing. Using competent personnel ensures compliance and accurate results.
What Should Be Included On A Test And Tag Label?
A proper test tag must include the tester’s name, the test’s date, and the next inspection due date. It should also clearly state whether the equipment passed or failed. This label should be placed in a visible spot on the equipment and be durable enough to last until the next scheduled test.